
PIC感光顯影覆蓋膜 (PIC Photo-imageable Coverlay)
PIC photo-imageable coverlay film can replace photosensitive development ink by lamination.
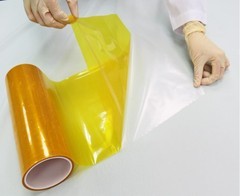
![]() |
產品詳細說明 Product details |
German FPCB factory uses PIC photosensitive developing coverlay film to replace photosensitive developing ink
Photosensitive developing ink construction is not easy to plug holes, the project is time-consuming and the yield rate is low.
The most troublesome problem in the FPCB industry for many years is solving the plug hole. This technical problem restricts Taiwanese manufacturers from entering the high-end precision FPCB market. If the Taiwanese FPC factory wants to enter the market controlled by the Japanese FPC factory, the application market of high-speed and fine hard disk drives, printers, precision medical, aerospace control, and the aforementioned technical problems of FPC It has to be solved first. However, this precise procedure requires several success factors. The first is that the soft board ink must be finely coated, soft enough to bend, and can eat the inner diameter of the fine hole wall to form protection. The second is that no matter whether the operator uses screen printing or roller coating, the technology of the builder must be good enough, otherwise, the probability of heavy work or poor quality is very high. Finally, the efficiency of the construction is not obvious, and the output scale and timeliness will be affected. stuck in a bottleneck. Europe, the United States, and Japan can be said to be the pioneers in the development of flexible circuit boards, and they are also the largest users of practical applications. In recent years, advanced material R&D companies in Japan, Europe, and the United States have begun to think about why we do not use the method of fitting to solve the problem that plug holes are not easy to succeed in. question. To solve this problem, the FPCB process time will be shortened, the material cost will be reduced by 1/3, and the product yield and output efficiency will be greatly improved. German TMT GMBH specializes in high-precision flexible circuit boards, which are used in high-end medical equipment and instruments. Due to the problems of solvent pollution and construction yield in the traditional photosensitive developing ink process, it has been actively seeking alternative environmentally friendly materials for a long time. TMT GMBH has begun to replace the developing ink with the PIC photosensitive developing overlay film of Taiwan Top Materials Technology. Taiwan factory developed PIC cover film to replace traditional photosensitive developing ink.
The soft board cover film is mainly used to cover and protect the fine circuit, make the flexible cable flexible and flexural, and protect the circuit from temperature, humidity, and polluting or corrosive substances. There are several types of soft board cover films developed so far: dry film type covering, screen printing type covering, and photosensitive developing type covering. Dry film type coverage and screen printing type coverage generally have the disadvantages of low yield, high cost, or insufficient precision and flexibility, and neither of them can fundamentally solve the quality problem of soft board plug holes. PIC photosensitive developable coverlay (Photoimageable Coverlay) has a higher technical level than dry film and screen printing. On the precise flexible circuit of the flexible board, the covered solder joints or connector joints need to be exposed. Therefore, the PIC photosensitive development cover film is more precise than the first two in terms of precise alignment, fine line spacing, and coating thickness. whichever is better. Therefore, the drilling holes on the soft board are not coated with soft board ink, but by lamination. Taiwan's TeamChem Materials Company has been engaged in the production and R&D of PIC Photoimageable Coverlay since 2012, and has now successfully mass-produced and exported to Europe. |